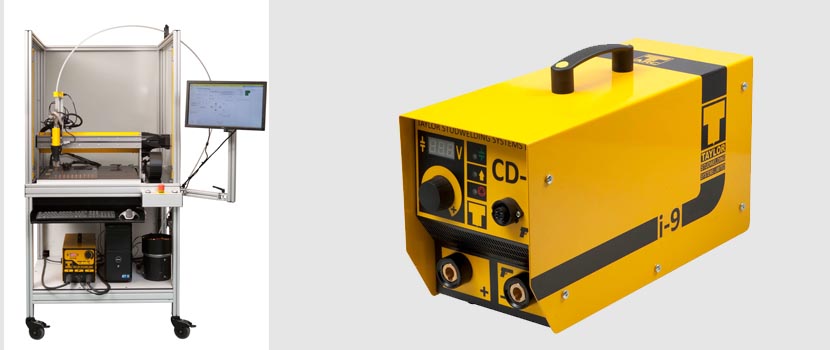
Stud welding is a specialized welding process that involves the attachment of a metal stud or fastener to another metal surface, typically a base metal or substrate. This process is commonly used in construction, manufacturing, and other industries where a strong and reliable connection between a stud and a workpiece is required.
Stud welding is a welding technique that facilitates the fusion of a metal stud with another metal surface. Typically, the stud is a metallic fastener featuring a flanged end or threaded tip. What sets this process apart is its ability to establish a robust and trustworthy connection without the necessity of supplementary materials like screws or rivets.
The fundamental goal of stud welding is to forge a durable and lasting bond between the stud and the foundational material. Widely applied across diverse industries such as construction, shipbuilding, automotive, aerospace, and manufacturing, stud welding proves to be a pivotal method for creating secure connections in various metalworking applications.
The stud welding process typically involves the following steps:
- Preparation:
The metal stud, usually with a threaded or unthreaded shaft, is positioned over the workpiece.
- Alignment:
The stud is aligned precisely with the desired welding location on the workpiece.
- Arc Initiation:
An arc is initiated between the tip of the stud and the workpiece using an electric arc or, in some cases, other methods like capacitor discharge.
- Melting and Fusion:
The intense heat generated by the arc melts the end of the stud and a small portion of the workpiece, creating a molten pool.
- Force Application:
Simultaneously with the melting, a spring-loaded mechanism or other force-applying method forces the stud into the molten pool, creating a secure and metallurgically bonded joint.
- Solidification:
As the molten metal cools and solidifies, a strong and durable connection is formed between the stud and the workpiece.
Stud welding offers several advantages, including rapid and efficient installation, minimal heat-affected zones, and the ability to create strong, reliable connections without the need for through-holes or additional fastening mechanisms. This welding technique is commonly used in applications where welding from both sides of the workpiece is not practical or accessible.
The equipment necessary for stud welding is crucial to ensure a precise and efficient process. The primary components required for stud welding include:
- Stud Welding Machine:
The core of the stud welding process, this machine generates the necessary electrical energy to create the arc for welding. It comes in various types, such as capacitor discharge, drawn arc, and short cycle, depending on the specific stud welding application.
- Welding Gun or Torch:
This handheld device holds and positions the stud over the workpiece. It also contains the necessary components to initiate the welding arc and drive the stud into the workpiece during the welding process.
- Collets and Ferrules:
These components are essential for securing the stud in the welding gun. Collets hold the stud, while ferrules guide the arc and help shape the molten pool during welding.
- Power Source:
Depending on the type of stud welding machine, a power source is required to supply electrical energy for the welding process. This can be in the form of electrical outlets for certain types of machines or dedicated power supplies.
- Grounding Equipment:
Ensuring a proper electrical ground is crucial for stud welding. This includes grounding cables and clamps to establish a reliable connection between the workpiece and the welding machine.
- Studs and Fasteners:
The specific studs or fasteners to be welded onto the workpiece. These come in various materials, sizes, and shapes, depending on the application and material of the workpiece.
- Protective Gear:
Safety equipment, including welding helmets, gloves, and appropriate clothing, to protect the welder from potential hazards such as sparks and UV radiation.
- Cooling Mechanism:
For certain applications, a cooling mechanism may be required to prevent overheating of the workpiece or the stud welding equipment.
Understanding and properly configuring these stud welding equipment components is essential for achieving successful and high-quality welds across various applications and industries.
What To Consider When Purchasing Stud Welding Equipment
When purchasing stud welding equipment, several key factors should be carefully considered to ensure you acquire the right tools for your specific needs. As a best welded studs suppliers in UAE ,Here are important considerations:
- Application Requirements:
Evaluate the specific applications for which you need stud welding. Consider factors such as material types, thicknesses, and the size and type of studs required for your projects.
- Welding Process:
Choose the appropriate welding process based on your application. The common types include capacitor discharge welding, drawn arc welding, and short cycle welding, each suited for different materials and project requirements.
- Equipment Type:
Select the type of stud welding machine that aligns with your applications. Portable, handheld units may be suitable for on-site work, while larger, stationary machines may be more appropriate for industrial settings.
- Power Requirements:
Assess the power source available in your workspace. Ensure the stud welding equipment’s power requirements are compatible with your electrical infrastructure.
- Stud Size and Material Compatibility:
Verify that the equipment can accommodate the size and material of studs required for your projects. Different welding machines are designed for specific stud sizes and materials.
- Ease of Use:
Consider the user-friendliness of the equipment. Look for features such as intuitive controls, easy setup, and ergonomic design to enhance operational efficiency and reduce the learning curve for operators.
- Durability and Build Quality:
Invest in equipment that is robust and durable. High-quality construction ensures longevity and reliable performance, even in demanding industrial environments.
- Safety Features:
Prioritize safety features, including thermal overload protection, grounding mechanisms, and safety interlocks. Ensure that the equipment complies with safety standards and regulations.
- Brand Reputation and Support:
Research and choose reputable brands with a track record of producing reliable stud welding equipment. Additionally, consider the availability of customer support, warranty, and maintenance services.
- Cost and Value:
Compare the cost of the equipment with its features and capabilities. Strive for a balance between affordability and the value the equipment provides for your specific applications.
- Training and Support:
Check whether the supplier offers training and support for the equipment. Adequate training ensures that operators can use the equipment effectively and safely.
By carefully considering these factors, you can make an informed decision when purchasing stud welding equipment, ultimately ensuring that the equipment meets the specific requirements of your projects and delivers reliable performance. When choosing Stud Welding Machines in UAE, you can experience the quality and excellence performance of machines compare to other countries.
To know more about Uses of Portable Chamfering Pipe & Plate bevelling machine in UAE