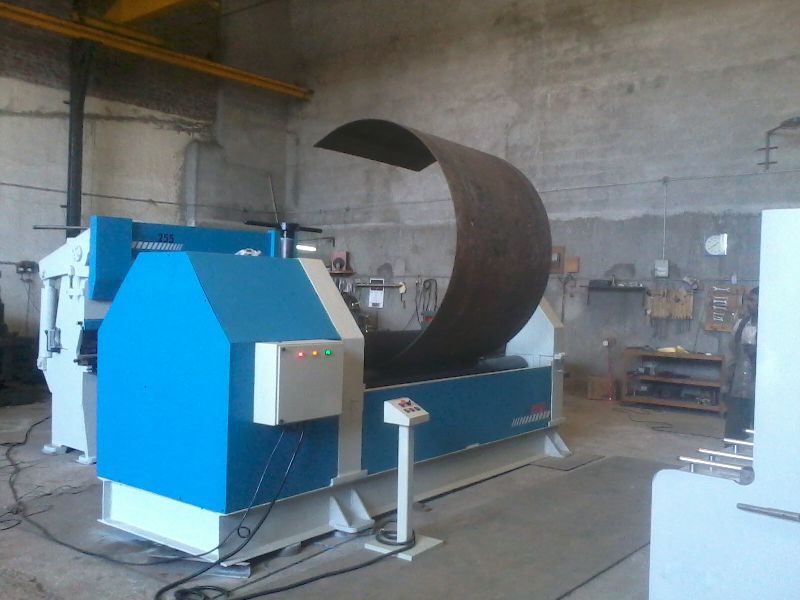
The steel fabrication industry in the UAE is radically and dynamically evolving. With more and more industries adopting advanced and automated metal working machines, like metal sheet rolling machines, the rate of turnaround time has improved significantly and enhanced the safety of personnel on the production floor.
The sheet rolling process, also known as roll forming, is a metal manufacturing technique widely used to shape flat metal sheets into desired profiles and shapes. In this process, the metal sheet passes through a series of rollers positioned in a specific sequence to bend and form the sheet into the required shapes.
Handling sheet metal rolling machines involves several potential safety hazards that operators and personnel need to be aware of. While operating sheet metal rolling machines, technicians should be careful to prevent accidents and ensure the well-being of other personnel on the floor. Let’s look into some common safety hazards associated with these machines and what steps help prevent them.
Moving Parts:
Roll-forming machines have moving parts, including rollers, that create pinch points. If operators are not careful, they can get their fingers, hands, or clothing caught or entangled between rollers, leading to serious injuries.
Distance from the machine:
Sometimes, the sheets that pass through the machines are released with unprecedented force. Rolling machines release debris like metal chips and sparks that can hit the personnel and cause injuries if they fail to maintain a safe distance from the machines. If the workers stand too close to the equipment, the product can potentially hit the personnel. Technicians might often need to work at heights and ladders while loading the equipment or adjusting the rollers. They need to be extra careful while working on elevated platforms.
Electrical Hazards:
Most industrial and steel fabrication machines run on high-voltage electricity and the floor safety managers should be extra careful about necessary protection measures. No one wants a short circuit in an industrial setup. Faulty wiring, improper grounding, or contact with live electrical components can be fatal and dangerous for the whole setup.
Faulty machine functions:
Accidental machine start-up, unsecured materials, improper sheet feeding into the rollers, failure to follow the safety protocols, and mechanical failures, such as jams or misalignments can lead to severe crushing injuries to the people on the floor.
Safety failures, Inadequate Training, and Maintenance
Insufficient training in operating the machine, safety procedures, and emergency protocols, or wearing proper PPE, such as safety glasses, gloves, or hearing protection can cause accidents that can otherwise be avoided.
Here are some safety tips to follow when using sheet metal rolling machines:
Training and Knowledge on using Sheet Metal Rolling Machines: Ensure that operators are trained in the use of the specific sheet metal rolling machine they are working with, including its operation, potential hazards, and safety protocols. Provide refresher training to operators periodically to reinforce safety practices and introduce them to any new safety features of the machine.
Protective Gear: Operators should compulsorily wear appropriate personal protective equipment (PPE) such as safety glasses, hearing protection, gloves, and appropriate clothing to protect against potential hazards.
Machine Inspection: Before using the machine, inspect it for any signs of damage or wear. Make sure all guards, covers, and safety devices are in place and functional.
Workspace decluttering: Keep the production floor clean. decluttered and organized. Remove clutter and obstacles that could interfere with safe machine operation or movement.
Machine Location: Placing the machine in a well-ventilated and well-lit area saves a lot of trouble. Ensure there is enough space around the machine for safe operation and maintenance.
Emergency Stop: Familiarize operators with the location and operation of the emergency stop button or switch. It should be easily accessible and functional.
Safe Distance: Maintain a safe distance from the machine while it’s in operation. Never reach into the machine while it’s running.
Roller Adjustment: When adjusting rollers or making changes to the machine setup, ensure that it’s properly shut down, and power is disconnected to prevent accidental activation.
Material Handling: Use appropriate lifting equipment, such as cranes or hoists, while moving heavy metal sheets onto the machine. Avoid lifting heavy loads manually.
Secure Material: Ensure that the metal sheet is properly secured and aligned before starting the machine. This prevents it from shifting during operation, reducing the risk of accidents.
Communication in Two-Person Operation: If the machine requires two or more operators for safe loading or operation, make sure they communicate effectively and follow established procedures.
Regular Maintenance: Keep the machine well-maintained by following the manufacturer’s recommended maintenance schedule. Regularly inspect and replace worn parts as needed.
Lockout/Tagout: Implement lockout/tagout procedures when performing maintenance or repairs. This involves isolating the machine from its power source to prevent accidental startup.
Supervision: Ensure that safety officers are present to supervise machine operation, especially for less experienced operators.
Reporting: Operators should make sure to report any safety concerns, near misses, or accidents to supervisors immediately.
Read more about uses from welded studs suppliers in UAE.